Introduction
In the field of manufacturing and construction, welding is a critical process that requires precision and reliability. Ensuring the quality and safety of welded joints is paramount, as flaws can lead to catastrophic failures. Traditionally, welding inspection has been a time-consuming and often reactive process, occurring after the welding has been completed. This approach can lead to increased costs, delays in production, and potential safety hazards if defects go undetected. A revolutionary development from Glasgow will transform the industry: the world’s first real-time welding inspection technology.
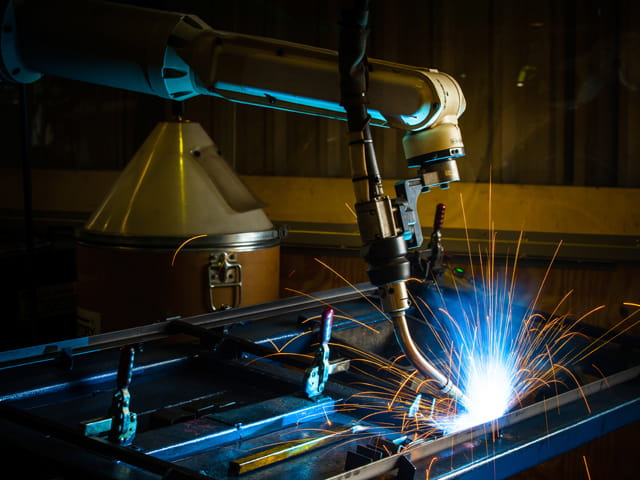
Glasgow’s Breakthrough in Welding Technology:
Engineers and researchers in Glasgow have achieved a significant milestone by developing the first-ever real-time welding inspection system. This cutting-edge technology enables immediate detection and assessment of welding quality; consequently, it marks a substantial leap forward in welding process inspection. Furthermore, the innovative welding quality monitoring system identifies defects as they occur, allowing for instant corrective measures.
The Glasgow-developed welding inspection tech harnesses advanced sensors and data analysis algorithms to continuously monitor the welding process. As a result, it provides real-time feedback to operators and quality control personnel regarding the integrity of the weld. Consequently, this breakthrough not only enhances welding efficiency but also significantly reduces the risk of structural failures from undetected defects, improving overall safety and reliability.
Advanced Welding Inspection Solution:
The real-time welding inspection technology developed in Glasgow represents an advanced solution that surpasses conventional methods. Traditionally, inspections rely on visual checks, radiography, ultrasonic testing, and other post-weld evaluation techniques. However, these methods can be time-consuming and often detect issues only after welding is complete. In contrast, the real-time approach offers immediate insights, greatly enhancing the overall efficiency and reliability of the welding process.
The Glasgow system uses cameras, thermal imaging, and acoustic sensors to monitor the weld pool and heat input. The system analyzes the collected data using sophisticated algorithms that can detect irregularities indicating a defect. This level of monitoring was previously unattainable during the active welding process.
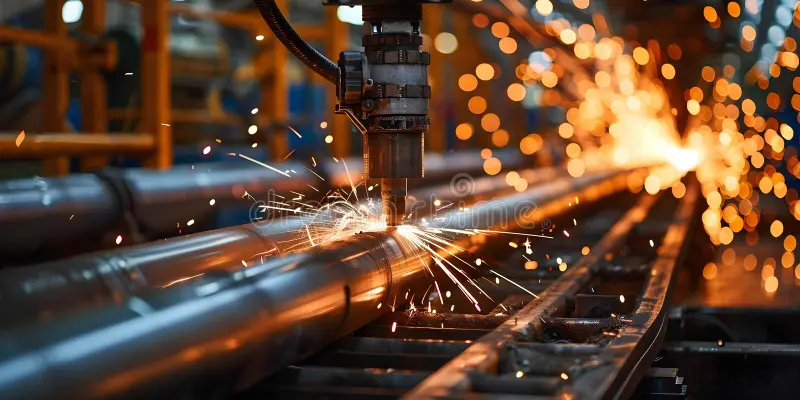
Welding Defect Detection in Real-Time:
A key advantage of the Glasgow welding inspection tech is its real-time detection of welding defects. This capability, in turn, allows for immediate intervention, reducing the need for costly rework or scrapping of materials. Furthermore, the system’s precision and speed enable it to identify various issues, including cracks, incomplete fusion, and incorrect weld profiles, ensuring higher quality and reliability.
As the welding torch moves, the system continuously updates the operator on areas needing attention. This instant quality control system ensures each weld meets strict standards and serves as a valuable training tool.
Innovative Welding Quality Monitoring:
The innovative welding quality monitoring aspect of the technology relies on machine learning and artificial intelligence (AI). As a result, as the system processes more welding data, it becomes increasingly accurate at predicting and identifying defects. Moreover, this self-improving feature makes the system more reliable over time, continually enhancing welding quality assurance.
The system’s ability to store and analyze welding data over time provides invaluable insights into welding operations. You can use this data to optimize welding parameters, improve workflow, and predict maintenance needs for welding equipment, enhancing operational efficiency.
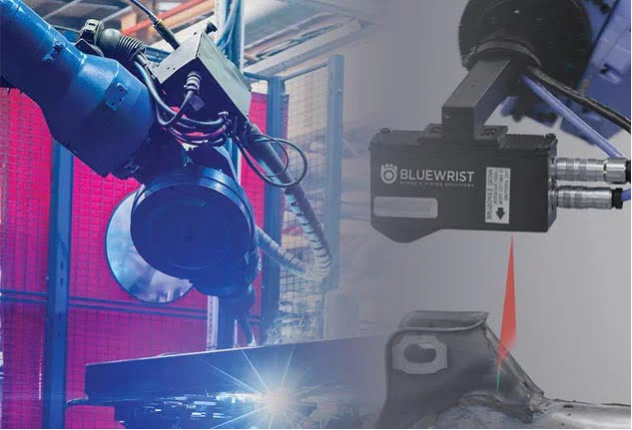
Cutting-Edge Welding Inspection Technology:
The technology’s non-intrusive nature ensures that it does not interfere with the welding process itself. It acts as an additional layer of quality control, offering peace of mind for manufacturers and constructors who depend on the strength and durability of welded structures. Its seamless integration into existing workflows enhances efficiency without disruption.
Revolutionary Welding Inspection Process:
This revolutionary welding process inspection technology will change the industry’s approach to quality control. Shifting from a reactive to a proactive stance on welding inspection allows companies to reduce production costs, improve product integrity, and enhance compliance with safety standards
The real-time feedback provided by the system can lead to better decision-making and more streamlined operations. Welders can adjust their techniques on the fly, and supervisors can make informed judgments about the continuation of work, all based on live data.
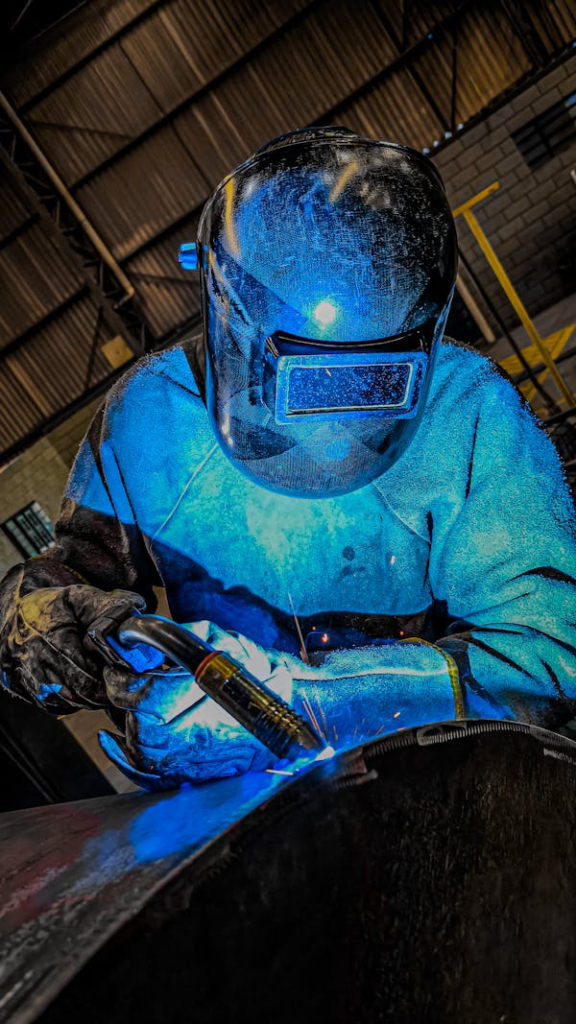
Conclusion:
The development of the world’s first real-time welding inspection system by Glasgow’s engineers is a game-changer for industries that rely heavily on welding. This Glasgow-developed welding inspection tech offers an innovative, advanced, and efficient solution for monitoring weld quality, detecting defects instantly, and ensuring the structural integrity of welded components.
As this cutting-edge welding inspection technology gains traction, it is expected to become a standard tool in quality control measures across various sectors. Glasgow’s breakthrough in welding technology showcases the city’s prowess in engineering innovation and sets a new benchmark for instant welding quality control systems worldwide.
The adoption of such technologies will lead to safer, more reliable products and structures, benefiting society as a whole. Companies looking to remain competitive and at the forefront of quality assurance will find Glasgow’s real-time welding inspection technology an indispensable asset in their manufacturing and construction processes.